Studio System™
Studio System™.High resolution printing. In-house & built to scale.
Overview
Studio System™ High resolution printing. In-house & built to scale. Introducing the Studio System+. Bringing new capabilities to the world’s first office-friendly metal 3D printing solution. The Studio System leverages BMD to deliver an office-friendly metal 3D printing solution. There are no loose powders or lasers associated with fabrication. In terms of support removal, parts are printed with their supports which are separated by ceramic interface media (or the Ceramic Release Layer™) that does not bond to the metal. This material disintegrates during sintering, making it easy to remove supports by hand

New features with Studio System+
The new system features the same office-friendly metal 3D printing as the original Studio System with new print capabilities and a scalable design for increased throughput.

Print at higher resolution
A new swappable 250μm printhead with supporting software profiles enables new geometries and applications—achieving smaller parts and fine features with an improved surface finish.

Watch a live stream of the build.
An in-chamber build plate camera captures video of the part as it prints — viewable in a web browser. This gives the user greater insight into their print and the ability to monitor print success.

Debind and sinter in bulk.
New stackable shelving increases part capacity of the debinder and furnace for greater throughput. Increased workload volume addresses bottlenecks typical at the debind and sinter stages.

Produce even better parts.
A new retort box design supports thermal uniformity—resulting in higher-quality parts.

Reduce operational costs.
External gas connections give the option to reduce the cost of consumables and achieve a lower cost-per-part.
Key applications for in-house metal 3D printing

Functional prototyping
Quickly move from design to prototype using production grade materials. Rapidly test and iterate to accelerate product development timelines and improve time to market.
Jigs & fixtures
Streamline assembly, joining, and inspection operations on your shop floor with 3D printed components. Quickly manufacture complex jigs and fixtures that can stand up to extreme manufacturing environments. (Download Case Study : Click)

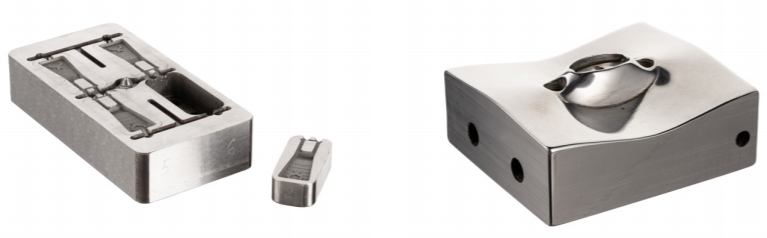
Manufacturing tools
Print tools to support a variety of molding, stamping, and extrusion applications. Utilize the near-net-shape capability of the Studio System™ to produce tooling components with greatly reduced post-processing. (Download Case Study : Click)
Low volume production
Replace cost-prohibitive setups and tooling, long lead-time castings and difficult machining operations by printing complex components directly with the Studio System™.

Materials
The Studio System™ is designed for multi-material compatibility and effortless material changes.Leveraging well-studied alloys from the Metal Injection Molding (MIM) industry, the Studio System™ materials are specially formulated into safe-to-handle bound metal rods, resulting in less shrinkage and higher sintering density than alternative extrusion-based technologies.
- 17-4 PH stainless steel for strength and corrosion resistance
- 4140 low alloy, mid-carbon steel for high strength and toughness
- H13 tool steel for hardness and abrasion resistance at elevated temperatures
- 316 L stainless steel for corrosion resistance at high temps
- Copper for thermal and electrical conductivity
- Alloy 625 superalloy for strength and corrosion resistance at high temperatures


Specification (Download Spec.)


Technology
The Studio System™ is designed around the chemistry and powder supply chain of the Metal Injection Molding (MIM) industry. Leveraging this mature, multi-billion dollar global industry gives Desktop Metal customers proven and reliable metallurgy. The images below show how the Studio System™ Hardware makes the Bound Metal Deposition™ (BMD) process accessible for users.

1. Perp
Secure, web-based software constructs build plans from STL or CAD files, automatically generating supports and control parameters based on part geometry and material.

2. Print
Layer by layer, a green part is shaped by extruding bound metal rods—metal powder held together by wax and polymer binders—in a process called Bound Metal Deposition™.

3. Depowder
The green part is immersed in proprietary debind fluid, dissolving the primary binder and creating an open-pore channel structure throughout the part in preparation for sintering.

4. Sinter
Depowdered parts are placed onto trays in a shop-safe, high-throughput furnace for batch sintering. With an external gas hookup and temperatures reaching 1400ºC, the Shop System furnace is able to deliver quality and reliable sintering in a shop-friendly format.
Software : A software-controlled workflow from digital model to sintered part

Fabricate™ delivers a seamless workflow for printing metal parts with the first office-friendly metal 3D printing system.
- Accepts native CAD files
- Auto-generated Separable Supports™
- Live tracking & alerts
- Interactive toolpath preview
- Multi-device management
- Custom fabrication plans